Definition of wood logs pellet production line
Using logs as raw materials, formed by solidifying and extruding into high-density pellet fuel through pretreatment and processing. It can save energy and reduce emissions, will make good economic and social benefits.
Raw Material:
There are mainly logs of pines, firs, acacia trees, beech trees, eucalyptus trees and other trees.
Now take the construction wood logs pellet production line project of 15tph as a case, according to the technological process and each section to do the following introduction and description.
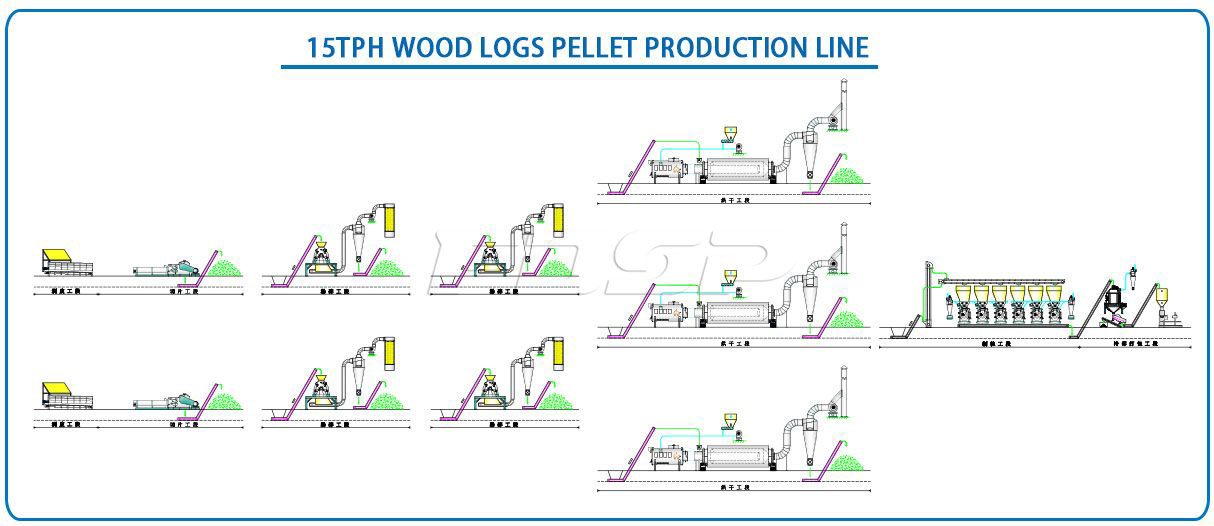
Introduction to flow diagram:
After debarking the branches and trunks of logs, the logs are cut into small chips by the chipper. The size of the chips is 20-30mm and the thickness is 5-10mm, then be fine grinded into sawdust of 3-4mm by the hammer mill; next the raw material is dried to about 15% through a three-layer drum dryer; finally is pelleted, the diameter of finished pellets is 6-10mm for choosing. After pelleting and cooling, it is packed into 20-50kg/ bag by small bag packing scale for convenient transportation and sale. The capacity of log pellet complete project is 15tph biomass pellets line, the total power of whole line equipment is about 3270 kw, and the plant covers an area of 6500 ㎡, including raw material storage and finished product storage. The whole line’s design is compact, the structure is reasonable, meets the requirements of environmental protection, and can be directed designed according to customers’ requirements.
Debarking Process---Chipping Process--Grinding Process--Drying Process--Pelleting Process--Cooling&Bagging Process
Craft features and process introduction
Debarking Process:Raw material debarking can improve heat value of finished pellets, reduce ash residue after combustion of finished pellets and reduce emissions.
Debarking Machine(2sets): LYBP900-II, power is 2*11kw, designed capacity is 8-10tons per hour.
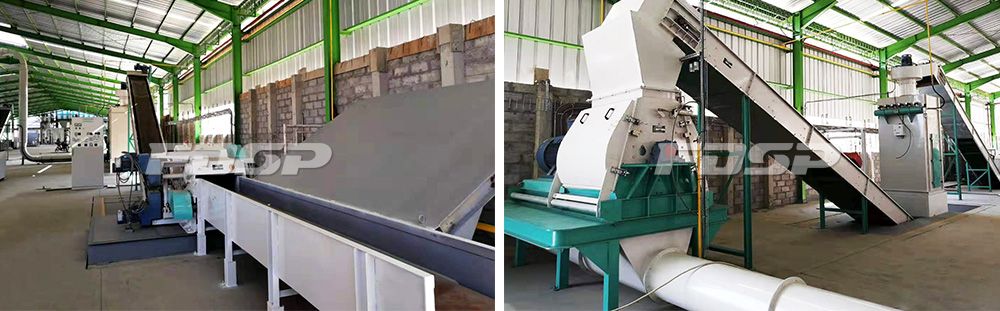
Chipping Process:The chipping process of the log pellet complete project is to process the wood logs into wood chips, the size is 20-30mm, the thickness is about 3mm, and then enter the processing of the following sections.
Chipping Machine(2sets): Chipper LYGX218D, power of main motor is 132kw, feeding roller is 4kw, oil pump is 0.55kw, designed capacity is 38m³/set.
Grinding process: The grinding work has no dust discharge. After grinding, the sawdust will be transported through pneumatic transmission by the fan suction air pressure. The hammer mill is a water droplet type structure; the hammer mill rotor can be operated in forward and reverse directions to improve the service life of the hammer blade; the direct transmission mode of the motor is adopted.
Grinding equipment(4sets): MFSP68*120,power 160kw,capacity: 6-8T/H( raw material moisture 40%)
Drying section: three-layer drum dryer, after drying, sawdust moisture in about 13-18%.
Drying equipment: LYHG50, drum diameter 3.0m, length 11.6m, power 19kw, design yield 5T/set, (before drying raw material moisture is 40%).
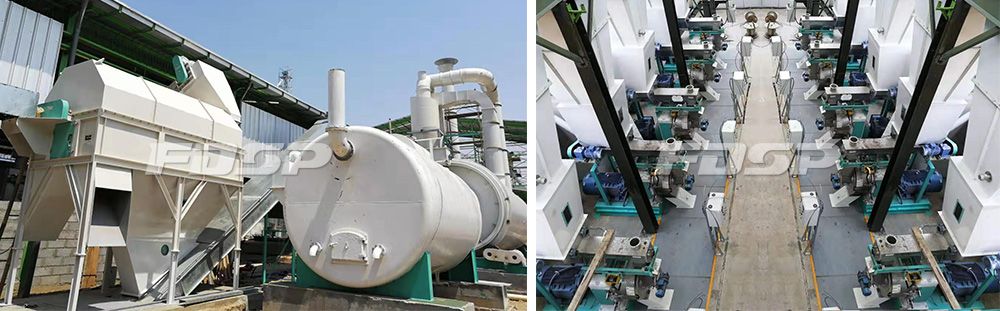
The diameter of biomass pellet is optional from 6-10mm, and the biomass pellets have the characteristics of high calorific value, no pollution and low ash content, which can be widely used in biomass power plants, biomass steam boilers, household fireplaces, drying furnaces and biomass gasifier.
Pellet mill(6sets): MZLH680, main motor power: 185kw, power of forced feeder: 1.5kw, design with 2.2-2.8T/set output.
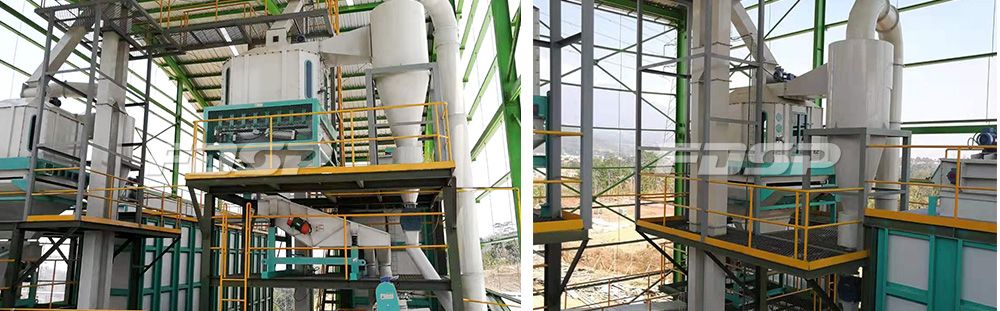
Cooling&Bagging Process: this is used to reduce the pellet temperature and moisture. After cooling through the cooler, the pellets temperature generally is not higher than room temperature 5℃, the moisture is about 8-10%, the density of pellets is 650-750 kg/m³. According to the local sales demand of the customer, choose the suitable packing scale to facilitate the customer to sell products. There are usually two specifications: small bag and ton bag. The packing specification of small bag packaging scale is 20-50kg/ bag, and the ton bag scale is 500-1000kg/ bag.
Cooling machine: MKLB8, the volume of the cooling chamber is 8m³, and the designed capacity is 12-15 tons per hour.
Packing machine: MDBLY-K, the packing specification is 20-50kg/ bag, and the packing speed is 3-5 bags/minute.
According to the needs of different customers, the scheme can be optimized:
1. If necessary, buffer bins can be added between each section to replace the storage yard. The advantage is that it can improve the automation degree of production line and reduce dust pollution in the workshop; The disadvantage is that it will increase the construction cost of the production line, and because the bulk density of materials after crushing is very light, it is easy to bridge in the bins and not drop.
2. The packaging equipment can be adjusted according to customers' requirements for finished product packaging. It can also be stored in bulk or silos.