Jiangsu Liangyou Zhengda Co., Ltd., specializing in the production of feed machinery and engineering, can provide customers with complete sets of equipment solutions for livestock feed (pig, etc.), poultry feed (chicken, duck, goose,etc.), ruminant feed (cattle, sheep, etc.), common aquatic feed (four major Chinese carps, etc.), special aquatic feed (shrimp, crab, etc.), extruded aquatic feed (floating and sink fish feed, shrimp feed, etc.), premix feed (including all kinds of additives, etc.), and pet food(cat food, dog food, etc.). to meet the different needs of customers.
Now take the Dual-line SZLH508(20tph) rabbit feed production line as a case, according to the process flow and each section to do the following introduction and description.
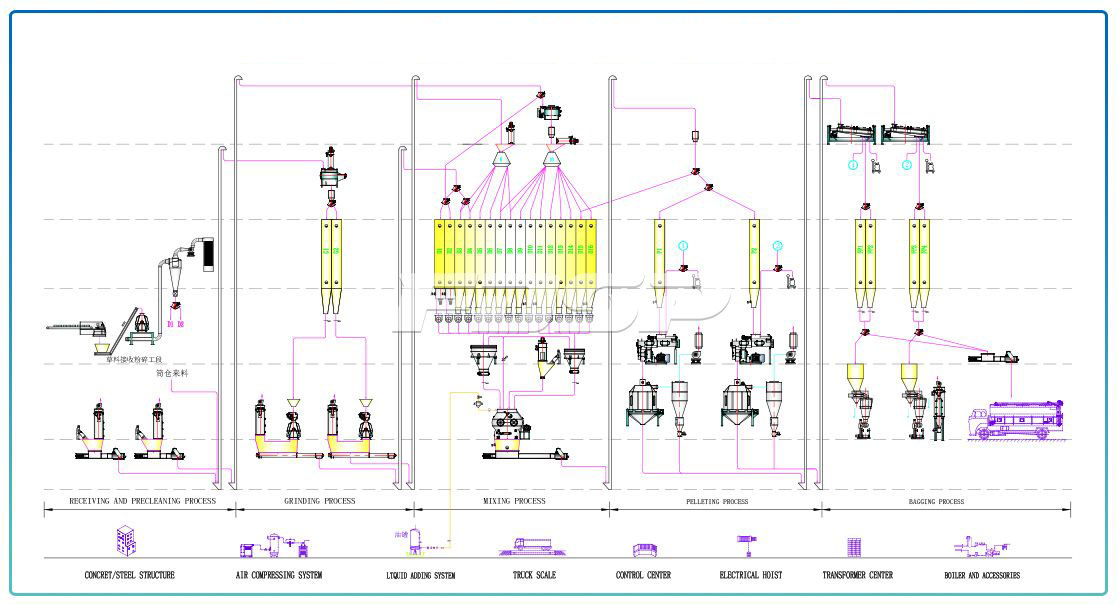
Raw material:
Conventional rabbit feed concentrate feed raw material include corn, wheat, barley, oats, sorghum, soybean, soybean meal, fish meal, amino acid, miscellaneous meal, fat, meat and bone meal, grain, feed additives and other feed raw materials of more than 10 varieties; In addition, according to the needs of different breeds and rabbits in different growing periods, alfalfa, straw and other forage or raw materials of coarse fiber can be added in the raw materials.
Brief introduction to the process:
Rabbit feed is characterized by moderate grinding fineness (screen hole diameter of 2-4mm), low requirements for curing and tempering (pellet mill adopts single-layer conditioner), and large diameter of finished particles (about 2.5-4mm in diameter). The dual-line SZLH508 rabbit feed is designed to produce 16-24 tph, with a single feed line of forage, two grinding lines, one batching and mixing line, two pelleting lines and two packing lines. The total power of the equipment is about 800KW; Construction area of the production area: 18×18×29.5m; Matching 2T boiler. The whole line has a compact design, reasonable structure, and meets the environmental requirements.
Process diagram:
Forage receiving and grinding process--Raw material receiving and cleaning process--Grinding process--Batching and mixing process-Pelleting process--Bagging or bulk process--Auxiliary process
Section introduction:
Forage receiving crushing section:
It is often necessary to add alfalfa, straw and other raw materials of coarse fiber in rabbit coarse feed.
Forage grinder: MFSP68×108, 55kw, side feed, output 3-5t /H; Secondary grinding: MFSP568 - Ⅱ, 37 kw, output 4-6 t/h.
Raw materials receiving and cleaning section:
In this section, pellet feeding cleaning and powder feeding cleaning are separated independently and separate dust removal. Dust removal effect is good.
Cleaning equipment:granules cleaner SCY80,capacity 20-30T/H;powder cleaner SQLZ60X50X100, capacity 10-15T/H.
Grinding section:
Because ruminant feed grinding fineness requirements are very thick,
this section adopts two small power hammer mills, and each sets allocated with two pre-grinding bins, which can grind different materials at the same time and improve the efficiency. Before entering the bins, the impurities are removed by magnetic separation device to ensure the safe operation of the hammer mill.
Grinding equipment(2sets): Hammer mill SFSP668×800, 55kw&75kw, designed to produce 15-20t /h/set(¢4.0mm screen hole)
Batching and mixing section:
This section adopts 16 batching bins( 2 bins are round bins for forage). Two sets of batching system work at the same time. It is developed by our company to realize accurate fast and slow feeding, fast batching and high precision.Because the formula contains a certain amount of grass flour raw materials, the proportion of grass flour is small, the volume is large, and it is easy to get into the roof, so the two grass powder bins discharge the material to choose the disc feeder, the discharge machine also chooses the large moel equipment, and the batching bucket is enlarged. At the same time, the batching sequence controlled by the batching program is optimized.
Weighing equipment: Dosing scale PCS20(customized and enlarged)/PCS05, dosing precision: dynamic ≤3‰, static ≤1‰.
Mixing equipment: mixer SHSJ4, (30KW, 2000kg/ batch), designed to produce 24-30t /h. Mixture uniformity CV ≤5%.
Pelletizing section:
This section adopts two sets of single-layer pelletizer, and each set with two pre-pelleting bins, which is convenient to switch between varieties. After pelleting, they are respectively entered into the cooler and the elevator into the rotary screener in order to be screened, and the finished products are put into the packing bins. The others are back to granulation or bags receiving. At the same time, the bulk trucks is designed to pack and transport.
Pelleting equipment(2sets) : SZLH508, 160KW, designed to produce 8-12t/h/set.
Cooling equipment(2sets) : SKLN6, designed to produce 10-15t/h/set.
Packing equipment: Belt scale (it can be used as powder feed or granule feed), packing range: 20-50kg/ bag, 6-8 bags/minute.
Auxiliary section:
Dust removal system to improve workers' working environment; Grease adding system, common mixer place added to improve feed palatability.
According to the needs of different customers, the scheme can be optimized:
1. The scheme adopts the single-point dust removal mode, that is, each rotary distributor (powder material) and pellet cleaner is equipped with a pulse dust filter, which has a good dust removal effect. Single point of dust removal is our company’s humanized design, which can provide a better working environment, but the cost increases. Customers can consider whether to use this configuration according to the actual needs;
2. According to the actual situation of the customer, whether there is forage added or not, so as to choose whether to configure or not.
3. The quantity of bins can also be adjusted according to the formula of customers, the characteristics of raw materials and other factors, so as to achieve the highest utilization rate and effectively control the production cost;
4. Dedusting design at the packing site can improve the working environment of workers, customers can be configured according to the needs